Compressed air isn't free, but we tend to forget about it
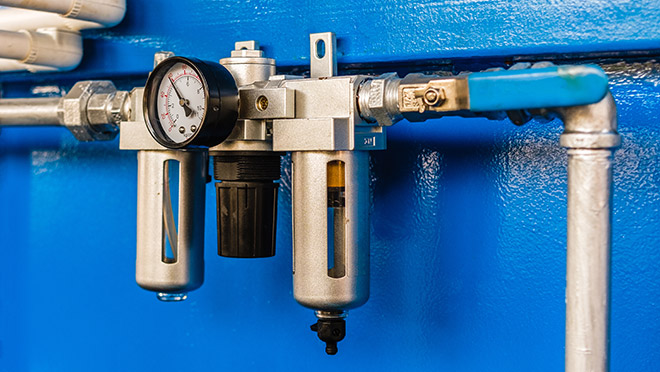
Up to 50% of compressed air can be lost through leaks
It only takes a quarter-inch hole in a compressed air line for 100 cubic feet of air to be lost in a minute. Given that it typically takes 20 kW of energy to produce that much air, the costs of a leak quickly add up.
That's just one fact showcased in a recent BC Hydro training session aimed at a collection of energy managers, operators, and vendors. For some, it was merely a reminder of why we should be paying attention to our compressed air systems. For others, it was a deep dive into a new world of potential energy savings.
"The inherent problem with compressed air systems is that they always leak somewhere," says BC Hydro's Steve Quon, who was on hand for the training led by compressed air guru Ron Marshall. "I don't think that's a surprise to people, but the challenge is to get them to plan for sustaining the repair of those leaks. It's not the most glamorous job, and the leaks show up all over the place, so it's kind of no fun."
Training leader Marshall is a veteran of 25 years of compressed air studies for Manitoba Hydro, and the eight hour training session gets into the gritty details of what those systems are all about. The main message is that facilities will waste a lot of energy and money if they don't use air compressor systems properly and don't maintain them regularly.
Quon says he worked in industrial facilities in the past where it wasn't unusual for workers to use compressed air hoses to blow away debris from machines, which he admits is fun in the way that it's enjoyable to clean a sidewalk with an air compressor.
"If you're using compressed air to blow down equipment, do you know how much it's costing to do that?" he says. "It's an awareness that there are inappropriate uses for it."
BC Hydro offers resources and incentives, to identify, investigate, and implement savings opportunities around compressed air systems. Vendors can also pitch in by helping facilities operators right-size systems and help implement variable speed drives and sequencing to allow for compressors to operate efficiently, and only when they're needed.
One of the more valuable parts of training is this 7-step action plan offered by Marshall:
- Develop a basic block diagram
- Measure your baseline and calculate energy use and costs
- Work with your compressed air system specialist to implement an appropriate compressor control strategy
- Once controls are adjusted, re-measure the baseline. Recalculate energy use and costs
- Walk through to check for obvious preventive maintenance items and other opportunities to reduce costs and improve performance
- Identify and fix leaks and correct inappropriate uses – know costs, re-measure, and adjust controls as above
- Evaluate Steps 1-6, implement awareness and continuous improvements programs, and report results to management.