Fan & pump systems
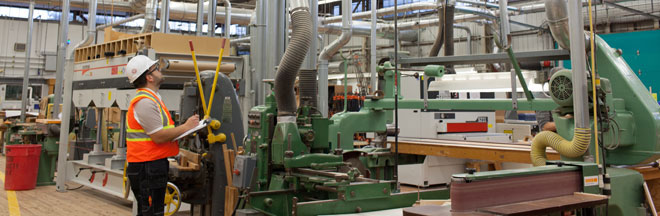
Optimize your fan and pump system
By improving fan and pump components and optimizing system requirements, a significant increase in the efficiency of the systems can be achieved. Pumping systems that move liquids, as well as convey materials, are often overlooked.
- Monitor fan systems
- Improve fan components
- Reduce flow resistance in fan systems
- Use high efficiency fan blades
- Maintain pump system and replace components if necessary
- Reduce overall pump system requirements
- Install variable speed drives for fans and pumps
- How energy management programs can help
Monitor fan systems
Improve operation and maintenance practices by regularly:
- Tightening belts
- Cleaning fans
- Changing filters
- Lubricating all electric motors, pumps and fans as needed
- Check alignment of fan belts and motors. Keep screens and guards in duct systems clean and clear of obstructions.
- Replace fans with more efficient models (types vary in efficiency depending on the application).
- Replace the standard V-Belt (efficiency is 90% to 97%) with a cogged belt (efficiency is 94% to 98%).
- Have your system properly designed to reduce air resistance.
Reduce flow resistance in fan systems
Increase the efficiency of your fan system by reducing flow resistance.
- Install turning vanes in square duct elbows or have elbows with as large a radius as possible.
- Ensure that ducts are clean and smooth.
- Make flow length as short as possible.
- Size ducts and other flow passages as large as is practical.
- Use inlet guards, filters and/or screens judiciously or you will waste energy.
- Use air filters only when necessary. Filters cause flow resistance and increase the fan's energy consumption.
- Use efficient flow control devices such as multi-vane dampers instead of single vane dampers (or better still-install an adjustable speed drive).
Use high efficiency fan blades
Typical fan blades used in refrigeration systems have an efficiency rating of around 40%. Better design can result in savings of approximately 15% of fan power.
Maintain pump system and replace components if necessary
- Inspect and repair all components of your system, such as bearings, lip seals, packings and other mechanical seals.
- Replace worn impellers (especially in caustic or semi-solid applications).
- Consider replacing typical pumps with more efficient models (newer pumps are 2% to 5% more efficient).
- You can reduce or control pump speed by trimming the impeller or changing gear drives to lower gear ratios.
- Replace throttle control valves with motor speed controls (e.g. adjustable speed drives) to meet variable loads (this typically applies to circulating pump systems, not systems with high static heads that use or have constant pressure).
- Match pump and motor size to better fit system load characteristics. Pumps are often 15% to 25% oversized. Have your pump supplier check your pumping system and replace oversized pumps with smaller ones.
Reduce overall pump system requirements
- Equalize flow over production cycle using holding tanks.
- Eliminate bypass loops and other unnecessary flows.
- Increase piping diameter to reduce friction.
Install variable speed drives for fans and pumps
Reduce your energy waste by installing variable speed drives, which create pump and fan and blower systems that respond to variations in demand. These systems only consume power when it's needed.
- Project Incentives. When a VSD system over 200 HP is necessary for your energy efficiency upgrade, it may be eligible for funding of up to 75% when bundled with other energy efficiency upgrades to your large pump or fan and blower system.
How energy management programs can help
If your fan systems aren't working efficiently, you may be paying for more than unused energy. That's because wasted energy doesn't just disappear – it damages dampers, increases bearing loads, and creates vibrations in ducts and seals, causing air leaks and failures.
All of that means poor performance and less reliability, ultimately increasing your maintenance costs and compromising your productivity.
Fan systems are rarely checked for efficiency and performance, which often leaves them drawing more power than needed.
With well-planned upgrades, you'll be left with a more efficient system that saves you money while running more quietly and reliably.
Program offers
Find out how your business can take advantage of generous funding for fans & blower optimization.
Eligibility criteria for programs below:
- Your system uses more than one gigawatt-hour of electricity per year, for a 200 horsepower system that's about 6,000 hours of operation.
Energy efficiency feasibility study
- An energy expert will conduct an in-depth study and evaluation of energy solutions within a single fans and blower system.
- The study provides the cost/benefit details you need to make strategic decisions.
Project incentives
- Implement energy saving equipment upgrades and efficiency projects.
- Get a fast return on investment with funding incentives and energy savings.
- Power Smart offers up to 75% funding of your upgrade costs.
- Incentive level and limits vary depending on your billing rate class (distribution vs. transmission).